When it comes to industrial maintenance, some companies see vibration analysis as an unnecessary expense, that is until they experience a costly equipment failure. One of our clients was on the fence about whether to implement a vibration analysis program. Instead of committing to a full program right away, they decided to start with an initial vibration summary. What we found saved them from significant downtime and potential financial losses.
Detecting the Problem Before It Became a Crisis
During our analysis, we focused on one of their most critical machines: the main extruder electric motor. The data showed clear signs of bearing damage, something that, if left unchecked, could lead to complete motor failure.
ng you from costly repairs or replacements down the line.
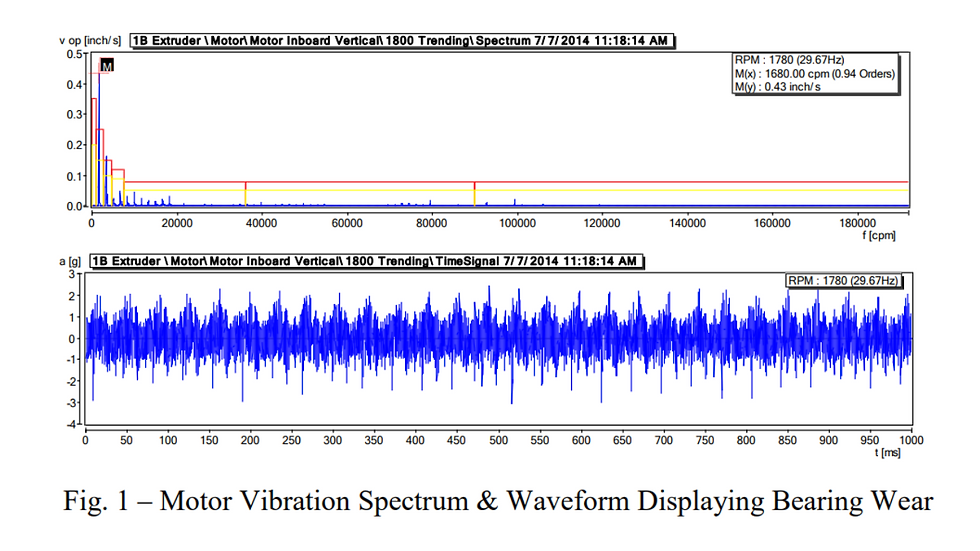

We immediately reported our findings to the client, who agreed to take proactive steps. Our team removed the electric motor, disassembled it, and confirmed the bearing damage. We then replaced the faulty bearings, reinstalled the motor, and performed a precise laser alignment to ensure everything was operating at peak efficiency.
No Production Loss, No Unplanned Downtime
The best part? We completed the entire repair during scheduled downtime on a weekend. The company didn’t lose a single minute of production. If the issue had gone unnoticed and the motor had run to failure, the facility could have faced extended downtime, emergency repairs, and significant financial losses.
Why Predictive Maintenance Matters
This case is a perfect example of why vibration analysis should be a routine part of any industrial facility’s maintenance program. Instead of waiting for something to break, we identify issues before they escalate. The more frequently you perform vibration analysis, the lower the risk of major repairs or catastrophic failures.
Think of it like going to the dentist—catching a cavity early is much easier (and cheaper) than dealing with a full-blown toothache. The same principle applies to industrial equipment.
Invest in Reliability
If your facility relies on electric motors and rotating equipment, implementing a vibration analysis program can help you avoid unexpected failures and keep your operations running smoothly. Our meticulous approach ensures that nearly every inspection uncovers opportunities for improvement.
Don’t wait until a breakdown disrupts your business. Reach out today to schedule your vibration analysis and keep your equipment running at peak performance! Contact Us Here.
Predict Industrial Reliability
Previously Predict Monitoring Systems
Welland, ON

Comments